В областта на осигуряването и контрола на качеството, особено в индустрии като производство, космонавтика и здравеопазване, термините „инспекция“ и „тестване“ често се използват взаимозаменяемо. Те обаче представляват различни процеси, особено когато става въпрос за напреднали технологии като напрРентгенови инспекционни системи. Целта на тази статия е да изясни разликите между инспекцията и тестването, особено в контекста на системите за рентгенова инспекция, и да подчертае съответните им роли в осигуряването на качеството и безопасността на продукта.
Системите за рентгенова инспекция са метод за безразрушителен тест (NDT), който използва рентгенова технология за изследване на вътрешната структура на обект, без да причинява никакви щети. Тези системи се използват широко в различни индустрии като електроника, автомобилостроене и видео опаковане за откриване на дефекти като пукнатини, кухини и чужди предмети. Основното предимство на рентгеновата инспекция е способността му да предоставя подробно изображение на вътрешните характеристики на продукта, което може да бъде задълбочено анализирано за неговата цялост.
Процесът, чрез който продукт или система се проверява в инспекционна камера, за да се гарантира, че отговаря на изискваните стандарти или спецификации. В анСистема за рентгеново изследване, проверката включва визуален или автоматизиран анализ на генерираните рентгенови изображения. Целта е да се идентифицират всички аномалии или дефекти, които могат да повлияят на качеството или безопасността на продукта.
1. Цел: Основната цел на проверката е да се провери съответствието с предварително определени спецификации. Това може да включва проверка на физическите размери, повърхностното покритие и наличието на дефекти. 2.
2. Процес: Инспекцията може да се извърши визуално или чрез автоматизирани системи. При рентгеновата инспекция изображенията се анализират от обучени оператори или усъвършенстван софтуер за идентифициране на всякакви аномалии. 3.
3. Резултат: Резултатът от инспекцията обикновено е решение за преминаване/неуспешно въз основа на това дали продуктът отговаря или не на установените стандарти. Ако бъдат открити дефекти, продуктът може да бъде отхвърлен или изпратен за допълнителна оценка.
4. Честота: Инспекцията обикновено се извършва на различни етапи от производствения процес, включително инспекция на входящия материал, инспекция в процеса и инспекция на крайния продукт.
Тестването, от друга страна, оценява ефективността на даден продукт или система при специфични условия, за да определи тяхната функционалност, надеждност и безопасност. В случай на системи за рентгенова инспекция, тестването може да включва оценка на работата на системата, нейното калибриране и точността на резултатите, които произвежда.
1. Цел: Основната цел на тестването е да се оцени оперативната способност на система или продукт. Това включва оценка на способността на системата за рентгенова проверка да открива дефекти или точността на произведените изображения. 2.
2. Процес: Тестването може да се извърши с помощта на различни методи, включително функционални, стресови и производителни тестове. За системите за рентгенова проверка това може да включва пускане на извадка от известни дефекти през системата, за да се оцени способността й да ги открива.
3. Резултати: Резултатът от теста обикновено е подробен доклад, очертаващ показателите за производителност на системата, включително чувствителност, специфичност и цялостна ефективност при откриване на дефекти.
4. Честота: Тестовете обикновено се извършват след първоначална настройка, поддръжка или калибриране на система за рентгенова проверка и се извършват периодично, за да се гарантира непрекъсната производителност на системата.
Моля, позволете ни да представим една от нашите компанииСистема за рентгенова проверка
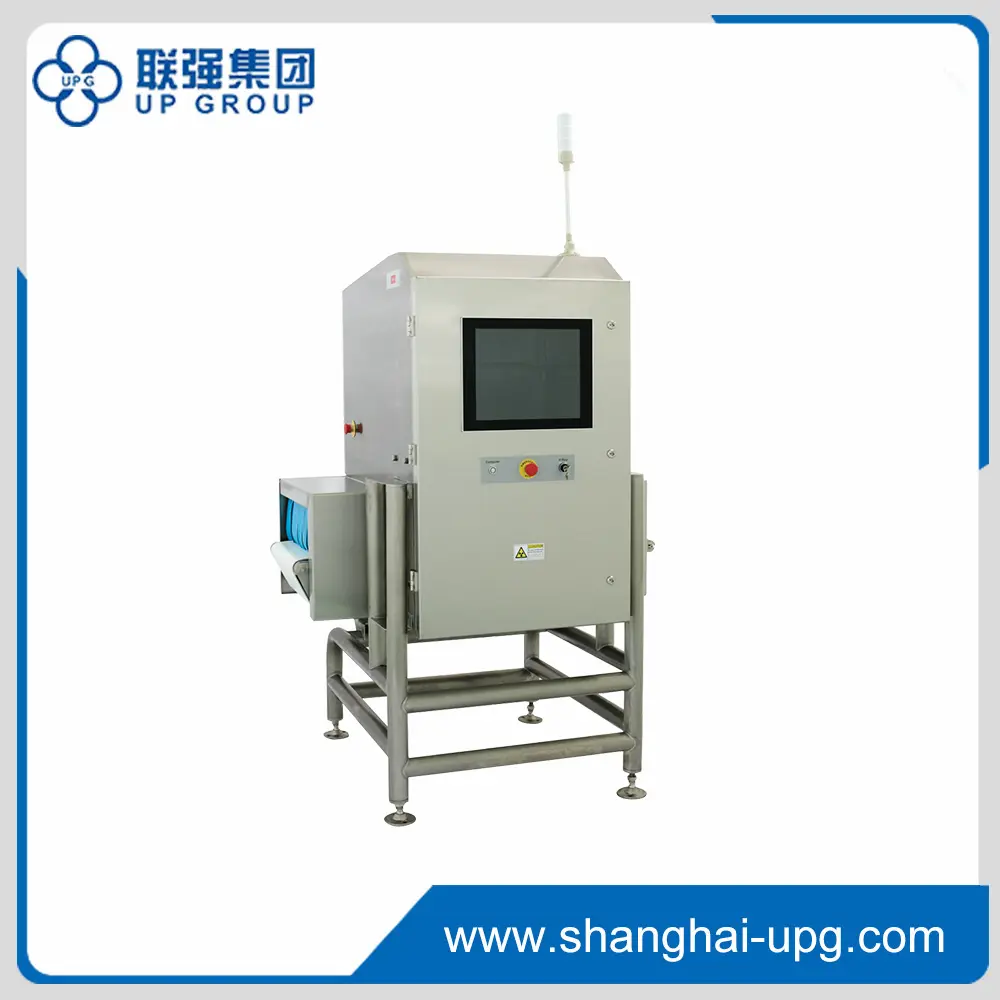
Базиран на интелигентни алгоритми за разпознаване на чужд обект с отлично софтуерно самообучение и точност на откриване.
Откриване на чужди предмети като метал, стъкло, каменна кост, гума с висока плътност и пластмаса.
Стабилен транспортиращ механизъм за подобряване на точността на откриване; гъвкав транспортен дизайн за лесно интегриране със съществуващи производствени линии.
Налични са широка гама от модели, като AI алгоритми, многоканални алгоритми, модели с широки модели за тежък режим и т.н., за да се подобри производителността и да се намалят производствените разходи на място.
Въпреки че проверката и тестването са важни компоненти на осигуряването на качество, те служат за различни цели и се извършват по различен начин и ето някои от основните разлики:
1. Фокус: Инспекцията се фокусира върху проверка на съответствието със спецификациите, докато тестването се фокусира върху оценката на производителността и функционалността.
2. Методология: Инспекцията обикновено включва визуален анализ или автоматизиран анализ на изображението, докато тестването може да включва различни методи за оценка на ефективността при различни условия.
3. Резултати: Резултатите от проверката обикновено са преминали/не преминали, докато резултатите от тестовете осигуряват задълбочен анализ на функционалността на системата под формата на доклад за ефективността.
4. Кога: Инспекцията се извършва на различни етапи от производството, докато тестването обикновено се извършва по време на настройка, поддръжка или периодична оценка.
В заключение, както проверката, така и тестването играят жизненоважна роля за ефективното използване на anСистема за рентгеново изследване. Разбирането на разликата между тези два процеса е жизненоважно за специалистите по осигуряване на качеството и контрол. Инспекцията гарантира, че продуктите отговарят на специфични стандарти и насоки, докато тестването оценява производителността и надеждността на самата система за инспекция. Използвайки и двата процеса, предприятията могат да подобрят качеството на продуктите, да осигурят безопасност и да поддържат съответствие с индустриалните стандарти. Тъй като технологията продължава да напредва, включването на усъвършенствани системи за рентгенова проверка във времето за осигуряване на качеството несъмнено ще играе ключова роля в бъдещето на производството и други индустрии.
Време на публикуване: 21 ноември 2024 г